I recently heard Amir Dan Rubin, president and CEO of Stanford Hospital & Clinics, describe the three plus year lean journey of his organization. While those in the audience were impressed and even
salivating over what they have accomplished, Amir was the first to say they have much more to do. A true journey it is. Even leaders from some of the organizations we want to emulate say they have many miles ahead on the lean journey.
What is lean? According to the Lean Enterprise Institute, “the core idea is to maximize customer value while minimizing waste. Simply, lean means creating more value for customers with fewer resources.”
Amir Rubin and John Shook, the CEO of the Lean Enterprise Institute – both national thought leaders in lean thinking – were the keynote speakers during the Healthcare Value Network (HCVN) site visit that the University of Michigan Health System hosted last month.
The network is a learning collaborative of health care organizations committed to lean transformation. UMHS is a founding member of the network. Attendees at this session included leaders from Stanford Health and Stanford’s Lucile Packard Children’s Hospital, Lehigh Valley, Cleveland Clinic, the BJC System, UMass and NY Health and Hospitals Corporation.
Our Michigan Quality System (MQS) actively participates in the network and organized the 2 ½ day site visit. MQS combines the strength and success of our longstanding commitment to scientific problem solving with tools and a unified philosophy to provide a robust approach to quality improvement. MQS adapts lean thinking as a consistent approach to quality and process improvement.
Led by Dr. Jack Billi, MQS has been helping UMHS make steady progress on our own lean journey for 8 years. Jack says he wants to develop 25,000 problem solvers – every UMHS employee. Our lean journey is evident throughout UMHS:
“Managing to Learn” courses focus on teaching A3 thinking by tackling a real problem with support of a mentor
- People work with a lean coach
- People develop a value stream for a functional area
- Groups implement daily huddles and visual boards
MQS staff and others showcased some of our more advanced areas of lean work at UMHS during this site visit.
Colleagues from other network member organizations also had the opportunity to visit a few outstanding companies in the Ann Arbor area to learn from them:
- Con-way Freight is a trucking company that is an exemplar in using their Visual Strategy room to manage their business
- Menlo Innovations is a software development company that has intentionally chosen to found its culture on the Business Value of JoyTM
- Last, but not least, Zingerman’s is known for its fabulous deli food and its unique culture – they offer training programs to other companies
Managing to Learn was one of the first training programs I attended at UMHS. I took on a project that turned out to be too big for a first A3 but, with the CEO as my mentor, I learned. Many of my management team and staff have attended lean training. We use standard forms for projects and capital requests that follow the A3 format – background, current state, problem, analysis, goals, and countermeasures. We still have room for improvement in true A3 thinking and problem solving. We track various metrics but don’t have a visual room or board where we regularly post such information to review it as a group.
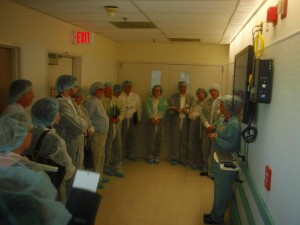
HCVN group Gemba visit to University Hospital OR huddle board. What went wrong today?
Gemba is a Japanese word which means “actual place”. In the process improvement context, “going to the gemba” means observing the process in action. Going to the “gemba” in my department is difficult; the majority of staff work in cubicles on computers. What exactly is the team’s process to observe and understand on a “gemba” walk?
I’ve been honest about the challenges in my own department, and I’m committed to applying lean methodology to our work. I look forward to the upcoming Lean Management On the Job Development (OJD) Program for senior leaders. One lesson I learned from Amir’s talk is this: senior leadership setting common expectations throughout the organization is critical to success. As we continue to roll out lean in IT, I expect everyone to participate. It needs to be embedded in everything we do. Lean will become the way we work.
Stay tuned for what I hope to be some of our own lean success stories.
See the Michigan Quality System website to learn about our health system’s lean journey: http://www.med.umich.edu/mqs/
See the UMHS Quality Improvement website for more information on UMHS efforts: http://www.med.umich.edu/i/quality/index.html
See the Virtual Lean Resource Center to learn more about lean: www.med.umich.edu/i/quality/tools/lean_assist.html